Process Improvement Plan
BLOG
11 min read
How to Create a Process Improvement Plan - A Step-by-Step Guide
Enterprises are always looking for new, innovative, and tech-supported modernized processes that can help streamline their workflows and operations. Many of them are still mired in outdated legacy systems with complex processes, making the overall experience taxing and affecting team productivity and efficiency. With technological advancements happening around, it is high time to choose digital enablers that can completely transform your existing processes.
As per a Salesforce research report, 74% of tech leaders believe that automation saves close to 50% of their time and helps reduce costs.
We already know that both the market and customer expectations are ever evolving. This makes it highly significant for service providers to be at the top of the list. One of the first steps towards this approach is adopting a viable business process improvement strategy. Implementing a whole new modernized business process may seem to be bumpy ride initially. We agree that there can be challenges. But for that we are here to help! We have created a comprehensive guide for you that can help in implementing the process improvement steps effectively. However, before we get to that, it is important to first understand what a process improvement plan is and how it can turn out to be a successful strategy for businesses. Let’s learn about it all and more in this blog.
What is a Process Improvement Plan?
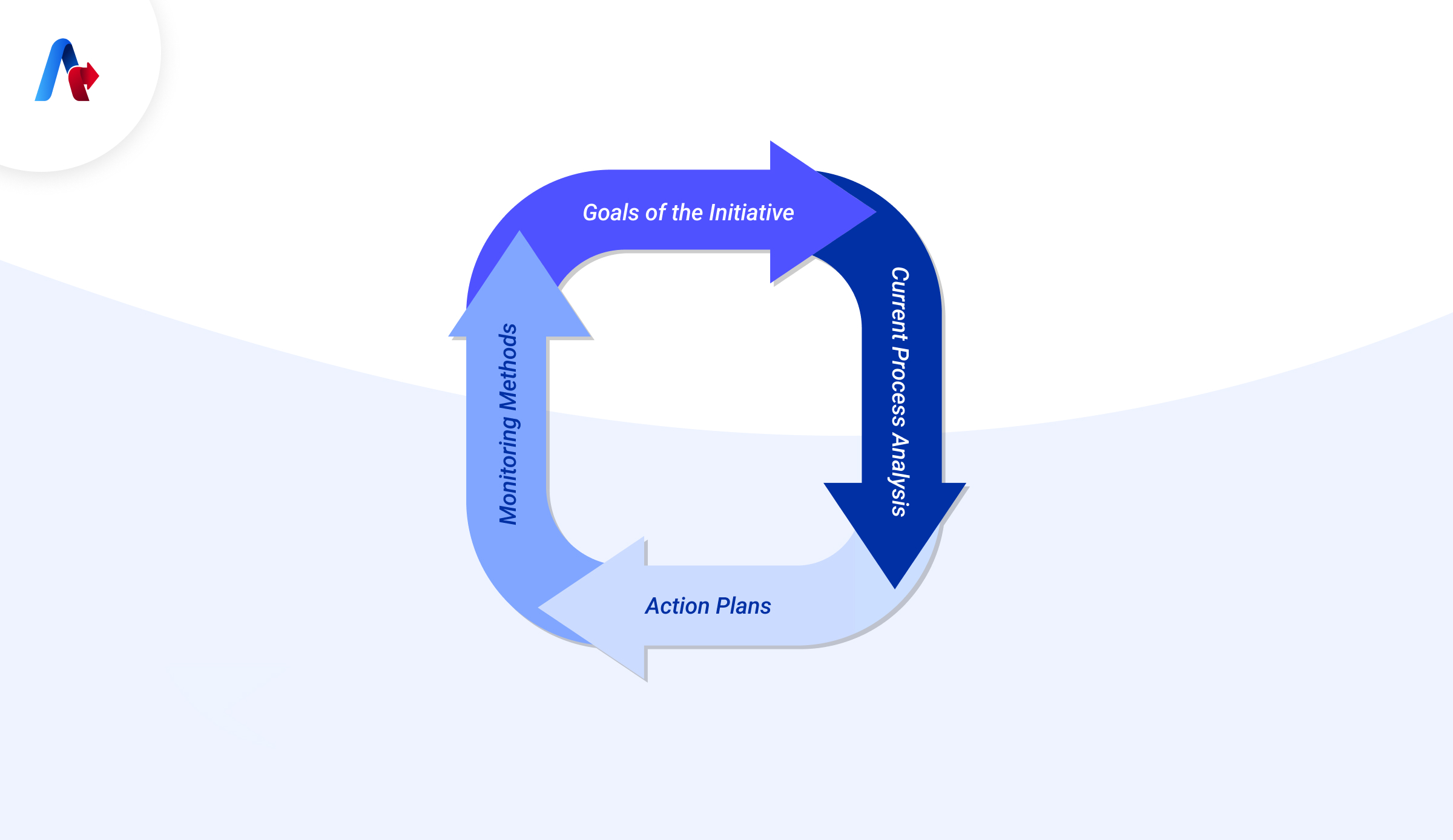
A strategic document, also known as a process improvement plan (PIP), lists every action that must be taken to improve an organization’s processes including performance, efficacy, and efficiency. It provides important background information on the current processes and workflows, performance metrics, and the areas of improvements. Typically, the PIP consists of:
- Goals of the Initiative: Clear and specific objectives that define what the organization aims to achieve.
- Current Process Analysis: A thorough rundown of existing workflows to find out inefficiencies and challenges.
- Action Plans: Comprehensive plans with deadlines and responsibilities for putting improvements into practice.
- Monitoring Methods: Strategies for keeping tabs on developments and measuring success.
A business process improvement plan guarantees that all stakeholders are in agreement and committed to accomplishing shared objectives by documenting these elements.
Why Is a Process Improvement Plan Important?
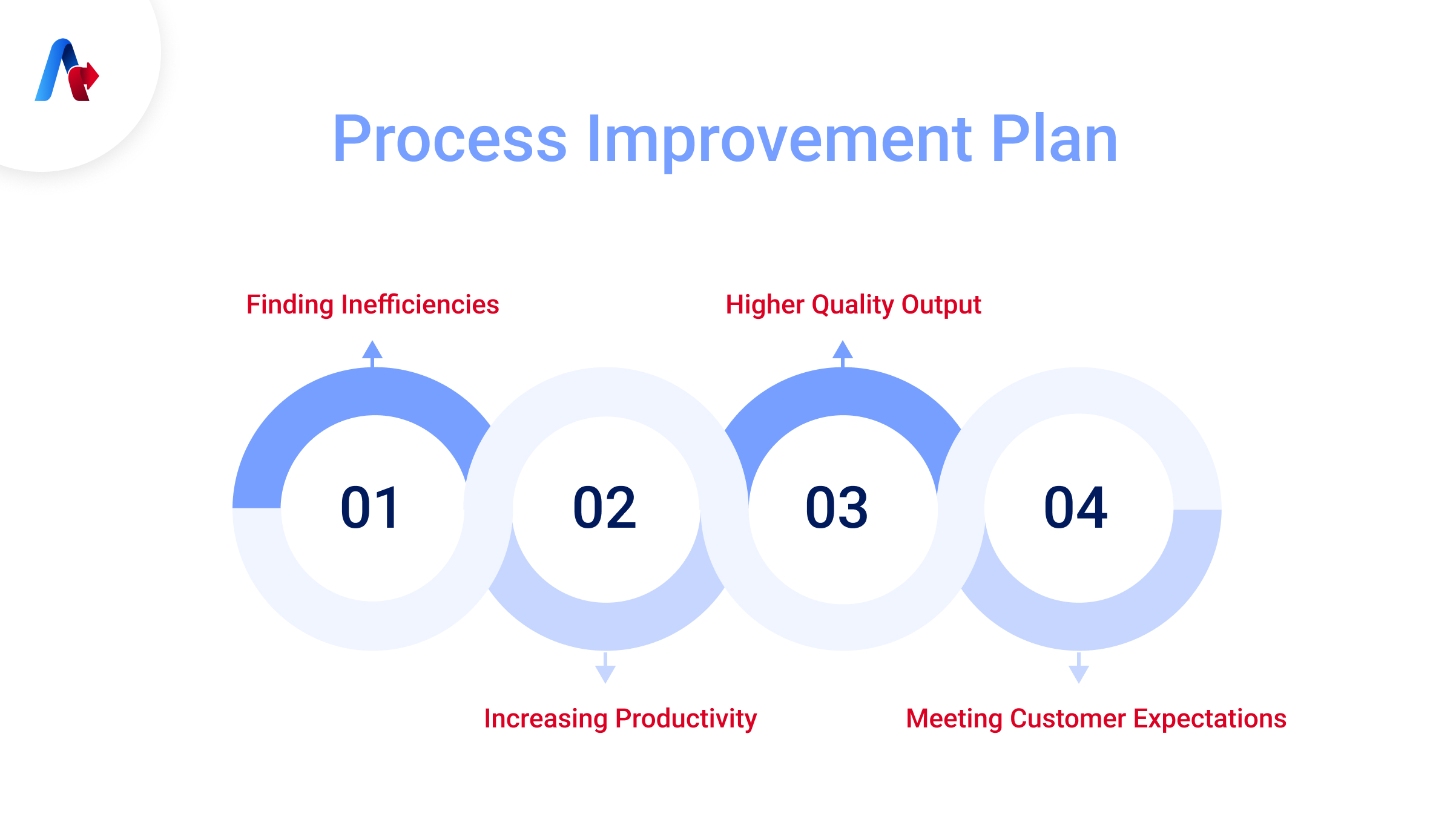
According to recent industry stat, enterprises that implement viable process improvement strategies can experience efficiency gains of up to 30% or more. This shows the impact of a well laid out process improvement plan on an organization’s success. Moreover, having a flexible business process improvement plan is essential for long-term sustainability given the quick changes in the industry and speed at which technology is developing.
Implementing a process improvement plan is needed for a number of reasons:
- Finding Inefficiencies: By assisting businesses in identifying areas where processes are lacking in terms of efficiency and require improvements, a PIP enables targeted enhancements.
- Increasing Productivity: Organizations can snip ineffective processes and improve team productivity with workflow improvements.
- Higher Quality Output: A well-executed PIP results in higher quality outputs by minimizing errors and increasing consistency.
- Including Teams in the Process: Engaging teams in the improvement process encourages a sense of ownership and can result in increased job satisfaction.
- Meeting Customer Expectations: Continuous improvements ensure that businesses can adapt to evolving client demands while maintaining high levels of service.
Steps to Create a Process Improvement Plan
Creating a successful and working process improvement plan involves a number of important steps. It was recently found that businesses with strong and reliable process management practices are more likely to report an increase in overall performance than those without it. This emphasizes the need to have a well-structured plan in place for process improvement.
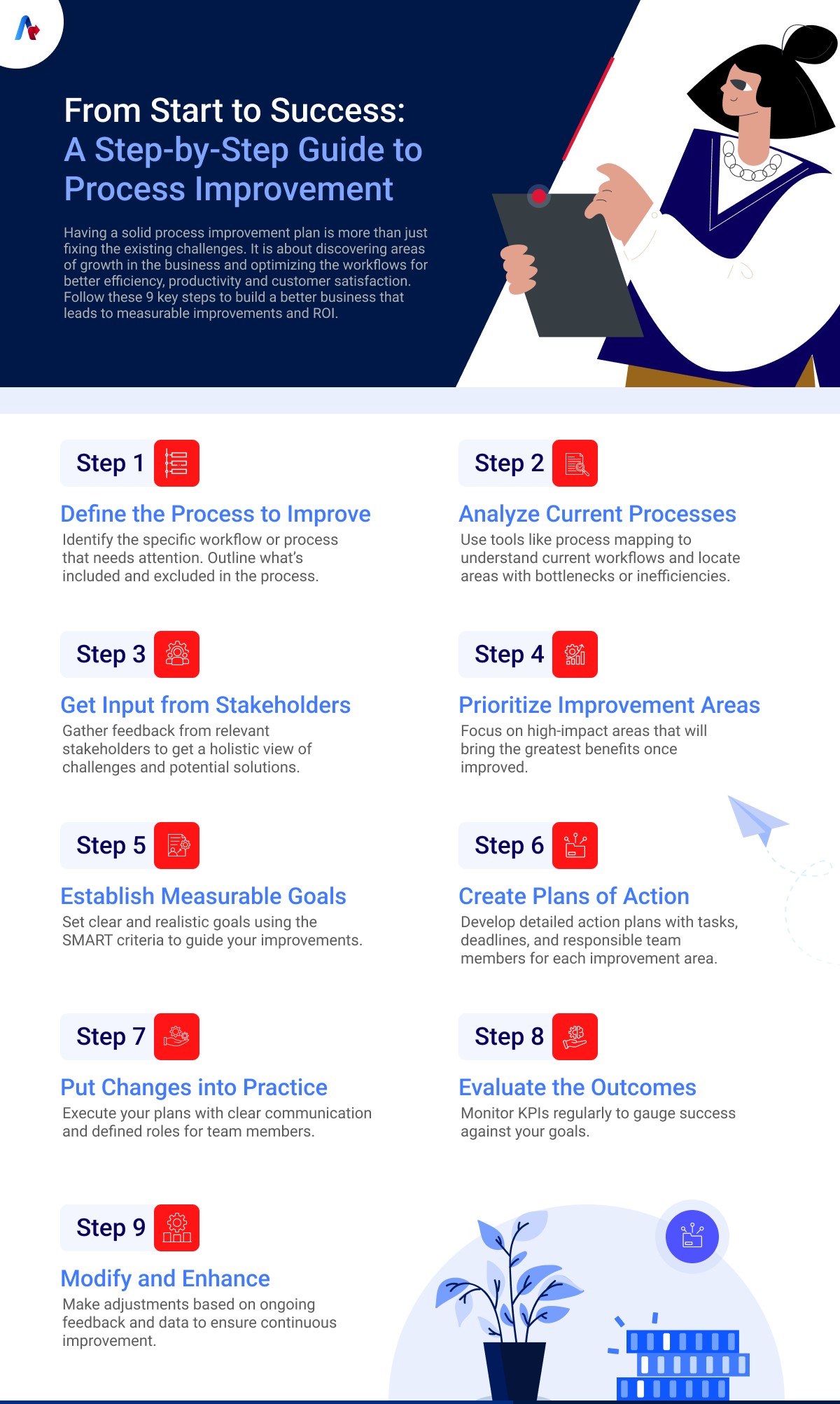
Here’s are some the key process improvement steps that can be considered to get started with it:
Step 1: Define the Process to Improve
Start by identifying which particular workflow or process needs to be improved first. This could include everything from managing inventory to processing customer service requests. Clearly outline what is and is not included in the process.
Step 2: Analyze Current Processes
Conduct a thorough analysis of existing processes for workflow improvement. Tools like process mapping can help you see and understand how information flows through your organization. Determine any obstacles, recurring themes, and underdeveloped resource locations.
Step 3: Get Input from Stakeholders
Engaging important stakeholders, including as management, employees, and other relevant parties, is the greatest way to address the challenges faced in your existing process. To get input on problems and possible fixes, conduct surveys or interviews.
Step 4: Prioritize Improvement Areas
Determine which areas need immediate attention by prioritizing them based on your study and stakeholder input. Concentrate on high-impact processes that, with improvement, will provide substantial advantages.
Step 5: Establish Measurable Goals
Set measurable, well-defined objectives for your development initiatives. These goals must to be time-bound, relevant, quantifiable, achievable, and targeted (SMART). For instance, set a six-month goal to cut customer complaints by 25%.
Step 6: Create Plans of Action
Make thorough action plans for every area that has been highlighted for improvement. Give team members tasks to complete, lay out the precise procedures that must be taken for implementation, and set deadlines.
Step 7: Put Changes into Practice
Carry out your action plans while keeping a careful eye on the results. Make certain that each team member is aware of their responsibilities during the implementation phase.
Step 8: Evaluate the Outcomes
Assess the effects of implemented changes on a regular basis against your set objectives. Monitor key performance indicators (KPIs) such customer satisfaction scores, cost reductions, and productivity gains.
Step 9: Modify and Enhance
Process improvement is an ongoing task. Always ask stakeholders for their opinions, and then incorporate changes as needed based on the new information and outcomes. These methodical process optimization steps guarantee that your company stays flexible and adaptable to shifting demands.
Process Improvement Plan Methodologies
At Accelirate, we think that successful process optimization requires a systematic and adaptable strategy. Our methods are intended to help companies identify inefficiencies, simplify procedures, and achieve sustained performance. Here are some of the best-known approaches that can be considered for the process improvement plan.
1. Robotic Process Automation (RPA)
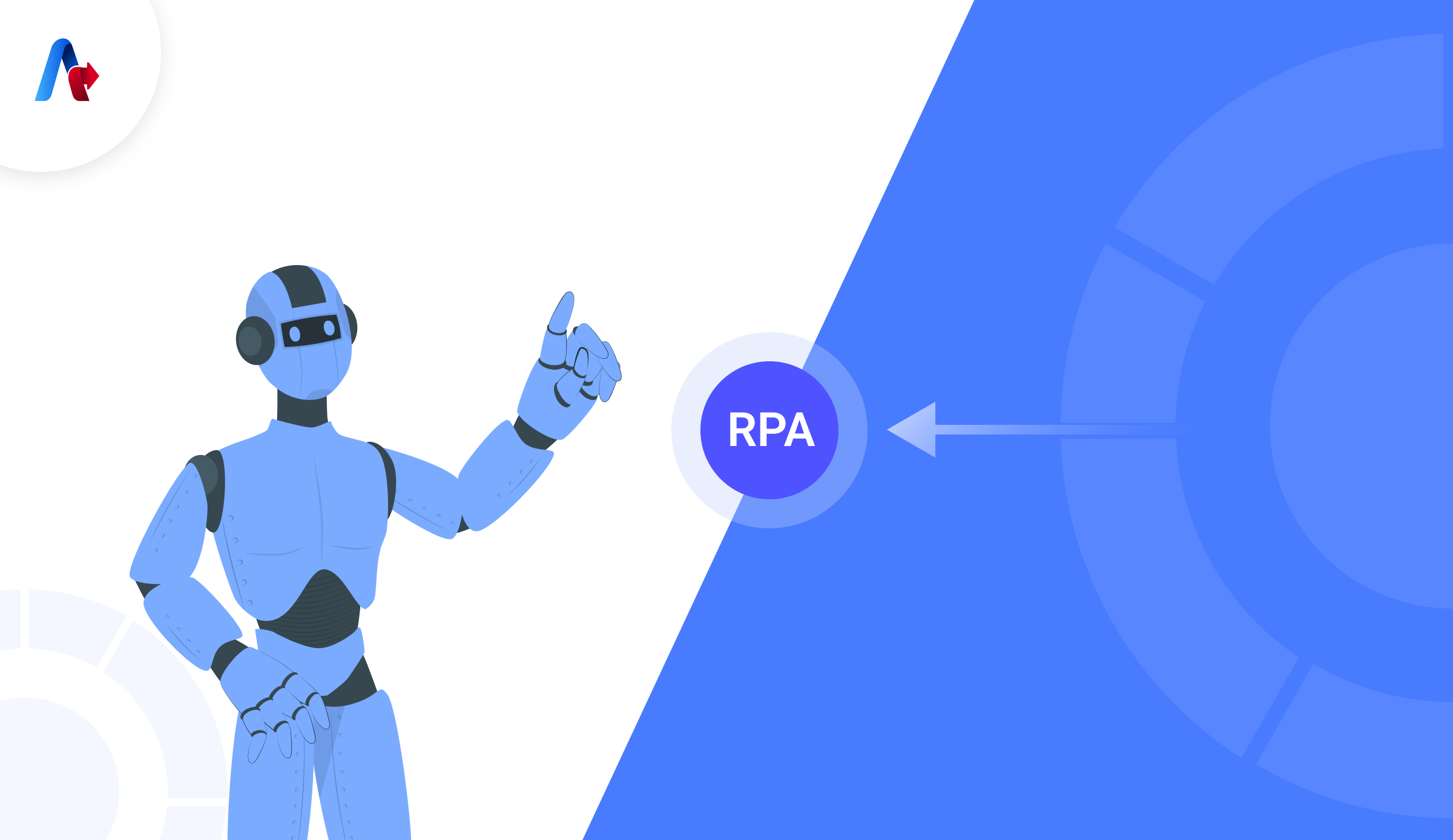
As a key pillar of our process improvement approach, Robotic Process Automation (RPA) enables enterprises to automate redundant, rule-based tasks that are typically taken up by people.
Key Features:
- Better Efficiency: Automates repetitive, time-taking jobs, allowing employees to concentrate and work on more critical tasks.
- More Accurate Results: Reduces common human mistakes, ensuring reliability and consistency in task performance.
Implementation Steps:
- Assessment: Identify processes that can be automated.
- Design: Create a thorough automation workflow.
- Deployment: Implement the RPA solution and monitor its performance.
- Optimization: Based on input and outcomes, continuously improve the automated procedures.
Did you know you can drastically cut operating expenses and increase productivity process automation?
Find Out How!2. Agile Methodology
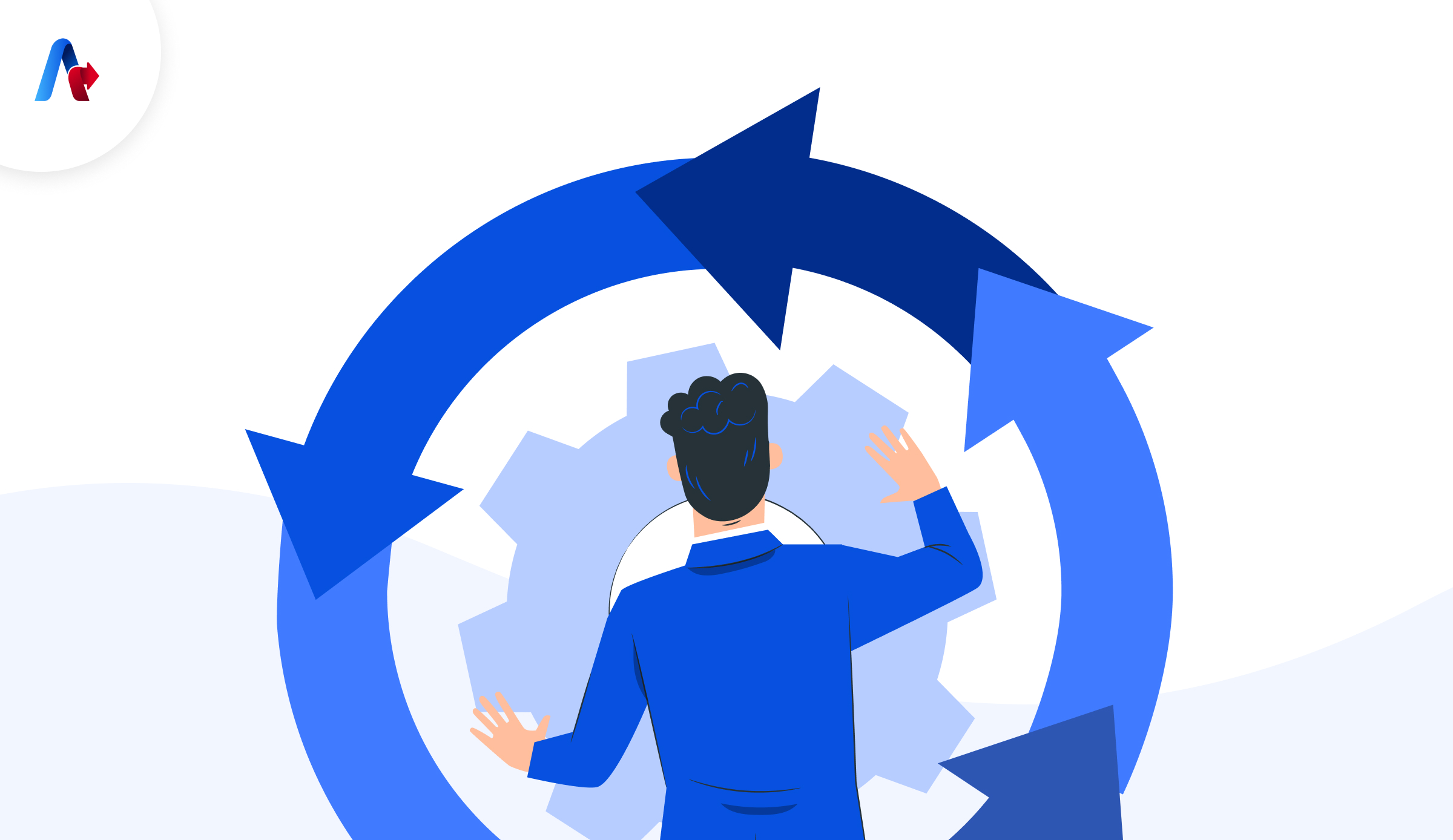
The Agile methodology works especially well in dynamic settings where requirements might change rapidly. It emphasizes adaptability, teamwork, and iterative development.
Key Features:
- On-going Process: Tasks are closed in short sprints, allowing enough time for regular reassessment and adjustments.
- Customer Focus: An Agile approach prioritizes delivering value to customers early and often, ensuring that their specific needs are met throughout the project lifecycle.
Implementation Steps:
- Sprint Planning: First, you must define what will be achieved in each sprint.
- Daily Stand-ups: Conduct quick meetings every day with teams and stakeholders involved to discuss progress and resolve any potential or existing issue.
- Review and Retrospect: Evaluate derived results and gather input for ongoing development at the end of each sprint for better visibility and decision-making at the end.
In short, Agile methodologies are one of the most reliable and preferred approaches by businesses to retain high-quality outputs while reacting quickly to shifting market needs.
3. Lean Six Sigma
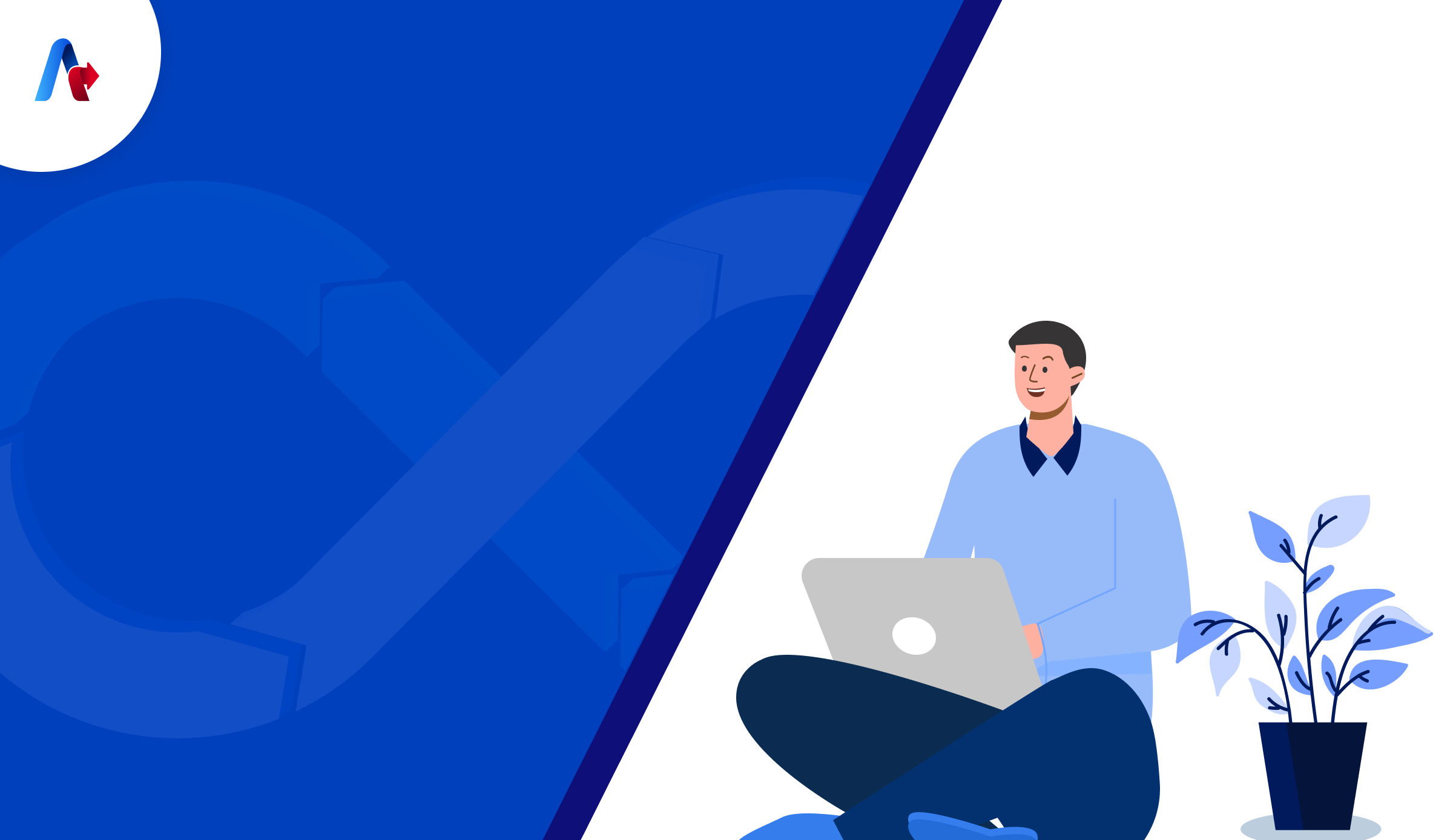
Lean Six Sigma blends Six Sigma quality control techniques with Lean production concepts. Through data-driven decision-making, this methodology prioritizes quality while removing waste, or phases in a process that are not productive.
Key Features:
- Waste Reduction: As a classic approach, this helps enterprises to identify and remove non-value-added activities from processes and make it more optimized.
- Quality Improvement: How do you identify the waste from an existing process? This methodology uses statistical analysis to improve the overall quality and reduce defects.
Implementation Steps:
- Define the Problem: First, you must clearly state the problem that you wish to solve.
- Assess Current Performance: Gather all the available information to determine how the on-going processes are operating.
- Analyze Data: Next is to identify the root causes of these errors and inefficiencies so that you can come up with a better resolution.
- Improve Processes: Once these defects are identified, implement solutions based on analysis findings that can help improve the process.
- Control Improvements: Monitor results to ensure sustained improvements over time.
In general, companies who wish to concentrate on both increasing quality and efficiency may find this methodology to be a perfect fit.
4. Kaizen, or Continuous Improvement
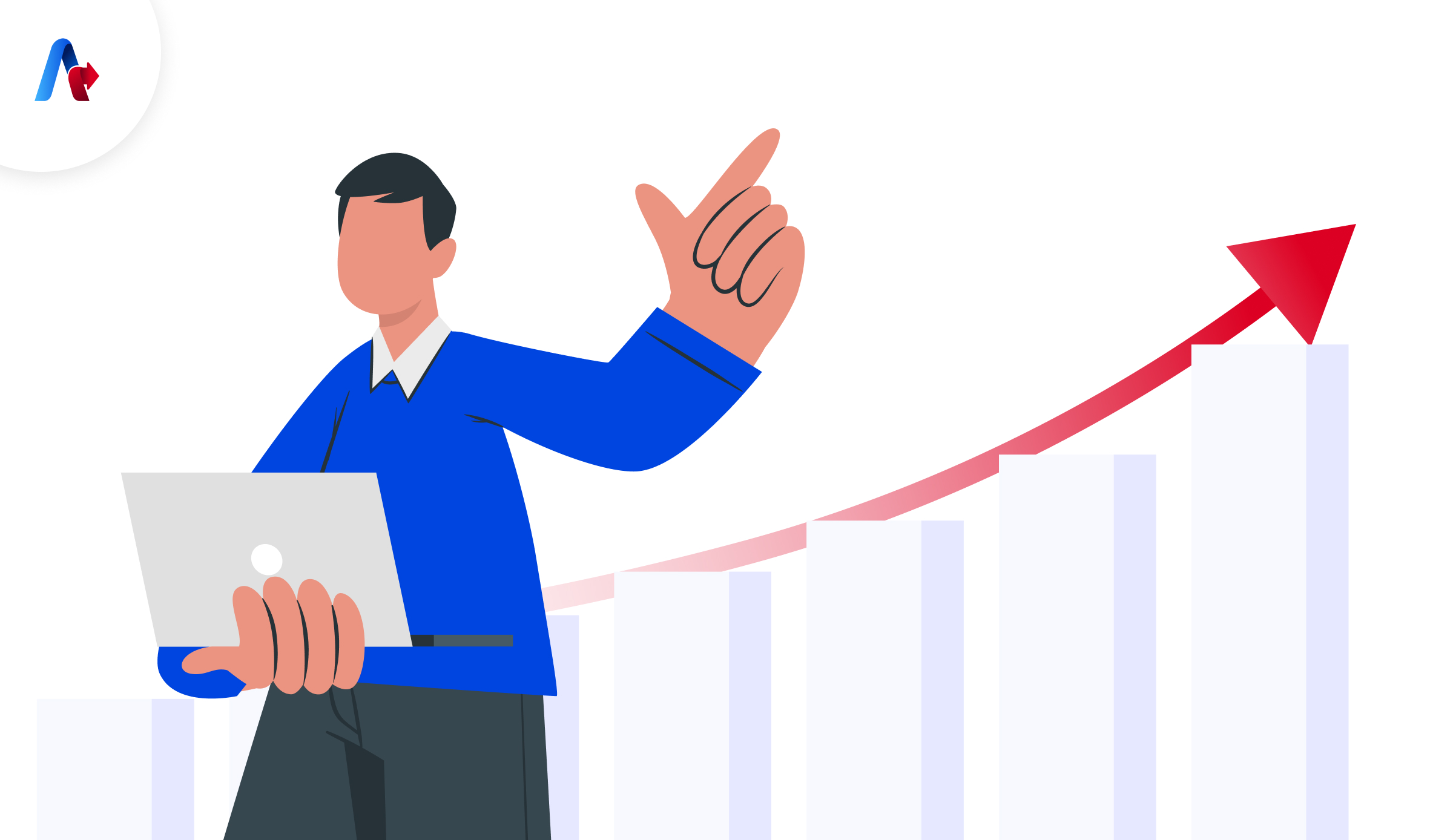
Kaizen, another name for the principle of continuous improvement, stresses making tiny, incremental changes that gradually result in larger ones. This strategy encourages all staff members to offer suggestions for enhancements.
Key Features:
- Employee Suggestions: All members of the organization are welcome to contribute to the process and offer suggestions for enhancements and modifications.
- Incremental Changes: This strategy emphasizes minor tweaks for better outcomes rather than concentrating on drastic changes all at once.
Implementation Steps:
- Innovative Team Sessions: Organize frequent workshops or brainstorming sessions where teams can suggest improvements.
- Trial and Error Method: Implement changes on a trial basis and monitor their effectiveness.
- Feedback Incorporation: Document outcomes and continue refining processes based on feedback.
- Continuous Improvement: Kaizen promotes a culture of ongoing improvement that improves overall organizational performance and occurs in the background.
5. Making Decisions Based on Data
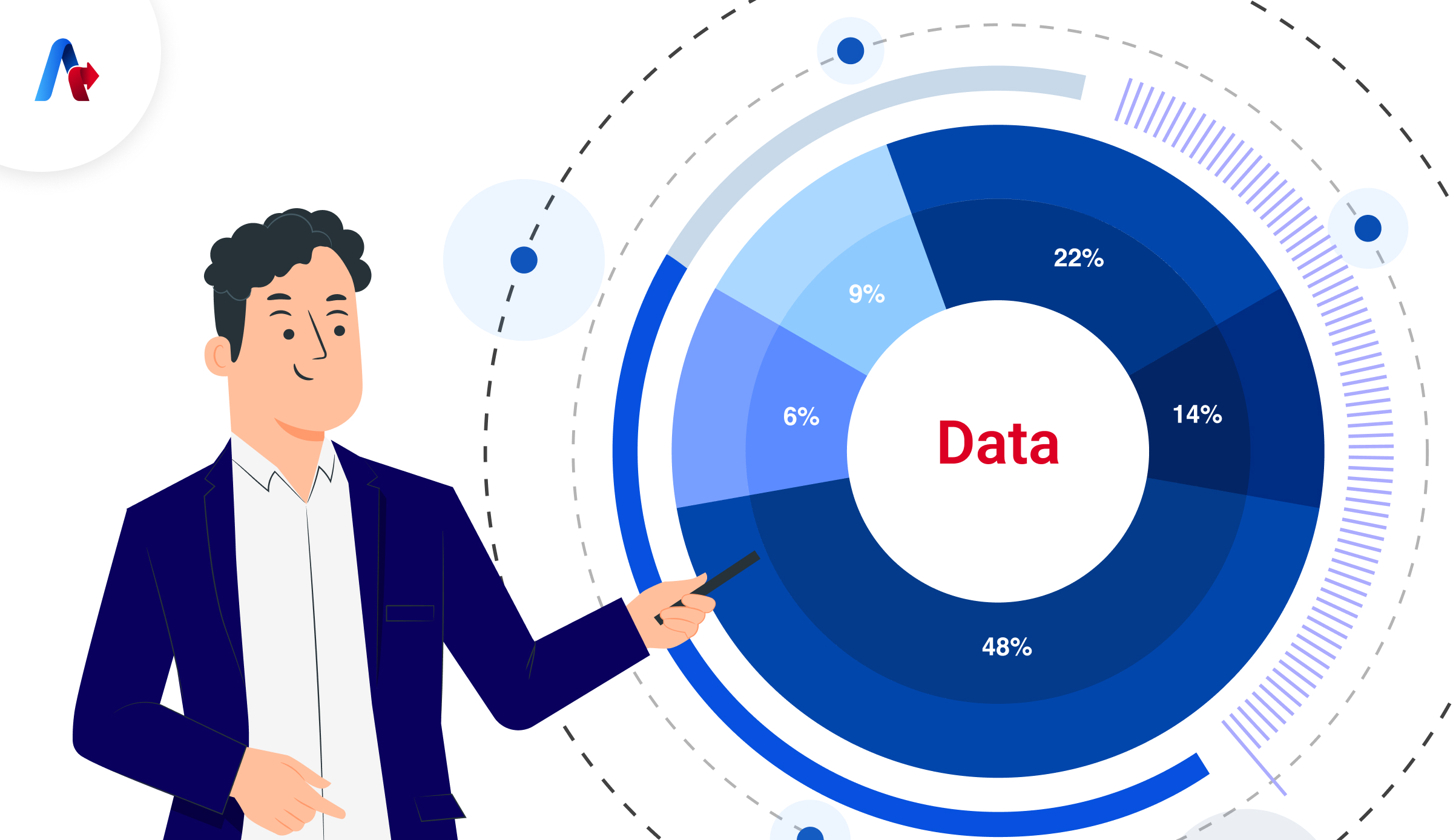
At Accelirate, we've always emphasized how crucial data is to advancing process enhancements. By using analytics and stats, businesses can make well-informed decisions based on current information rather than conjecture.
Key Features:
- More Well-Aware Decisions: This approach makes use of data analytics to identify patterns, inefficiencies, and opportunities for improvement.
- Performance Metrics: Key performance indicators (KPIs) are roped in the plan to accurately measure success and work on areas of improvement accordingly.
Implementation Steps:
- Define Goals: Identify relevant data sources and metrics that align with your business goals.
- Data Analytics: Use analytical tools to gather insights from data.
- Data Analysis: Use data analysis to back your judgments rather than just your gut feeling.
- Data-Driven strategy: By using a data-driven strategy, organizations can enhance their decision-making procedure and get better outcomes.
Utilize Accelirate's Strategic Process Improvement Plan to Streamline Your Workflows
Any organization hoping to improve their operations successfully needs a well-designed process improvement plan. You can start by developing a thorough plan using the steps and methodologies shared above to identify how the improved business process can result in increased productivity and efficiency. With a viable approach and well-suited strategy, businesses will be able to scale and minimize operational expenses. At Accelirate, our dedicated teams work alongside you at every step of the way and ensure that your process improvement journey is on track and is up for long-term success.
Want to learn how we can help transform your business processes?
Reach Out to Us Today!FAQs
Simplifying departmental communication with collaboration tools like Slack or Microsoft Teams, automating manual customer service tasks with chatbots, or switching from paper-based to digital documentation with document management systems are a few examples.
The DMAIC framework used in Six Sigma projects, Lean principles that emphasize waste reduction, Six Sigma that emphasizes quality enhancement, Total Quality Management (TQM) that emphasizes continuous quality improvement, Agile methodologies that encourage iterative development, Kaizen that emphasizes continuous incremental improvements, Business Process Reengineering (BPR) that involves radical redesigns, and others are common types.
Using tools like process mapping or root cause analysis, process improvement entails analyzing current workflows, obtaining stakeholder input through surveys or interviews, implementing changes based on action plans created from this analysis, measuring results against predetermined objectives, making necessary adjustments based on feedback received during implementation phases, and creating an environment that encourages ongoing learning among staff members involved in this journey toward improved operational capabilities over time!
Benefits include greater flexibility in response to market changes, primarily due to changing consumer preferences over time; lower operational risks associated with obsolete practices being replaced by modernized approaches better suited to today's demands on organizations; improved quality leading to higher customer satisfaction rates; and increased employee engagement due to involvement in decision-making processes!